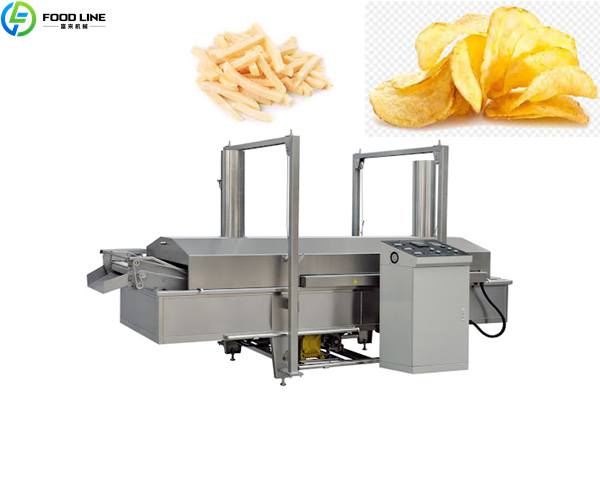
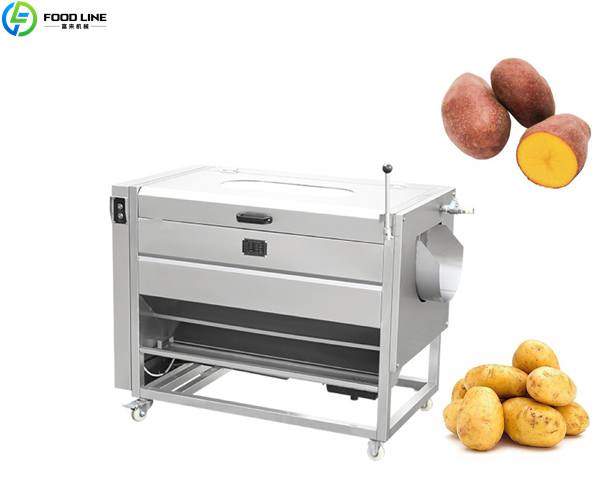
The equipment of this 100kg fully automatic chips making machines are made of SUS304 stainless steel. These machines meet the strict hygiene standards. And they have excellent durability and corrosion resistance. The production line integrates eleven key equipment to realize the full process automation of potato chips from raw material processing to finished product packaging, with a daily processing capacity of more than 100kg. If you want to know more about this production line, please contact us. Whatsapp/Phone: +86 13838385752.
Parameters of Machines
Equipment | Dimensions (L×W×H) | Power Specification |
---|---|---|
Lifting Feeder | 2500×630×1650 mm | 0.55 kW / 380 V / 50 Hz |
Brush Cleaning & Peeling Machine | 2600×850×1650 mm | 4.55 kW / 380 V / 50 Hz |
Picking Line | 4000×730×780 mm | 1.5 kW / 380 V / 50 Hz |
Imported Slitter | 1070×560×900 mm | 1.5 kW / 380 V / 50 Hz |
Soaking Hoist | 2500×1000×950 mm | 0.55 kW / 380 V / 50 Hz |
Burr Roller Trash Remover | 2500×1000×1350 mm | 1.5 kW / 380 V / 50 Hz |
Blanching Line | 3500×1150×2020 mm | 83.55 kW / 380 V / 50 Hz |
Air Cooled Dehydrator | 4000×950×1600 mm | 3.75 kW / 380 V / 50 Hz |
Fried String | 3000×1160×2200 mm | 123.55 kW / 380 V / 50 Hz |
Vibration Deoiling Machine | 2000×1450×800 mm | 0.26 kW / 380 V / 50 Hz |
Air Cooled Deoiling Line | 4000×950×1600 mm | 0.75 kW / 380 V / 50 Hz |
100kg Fully Automatic Chips Making Machines Advantages and Features
- Double mixing system, consistent quality: The core mixing system adopts a patented design that combines revolution and rotation. The mixing paddle can be flexibly disassembled and replaced to easily adapt to the processing needs of potato chips of different thicknesses and shapes. The mixing is more uniform and the performance is more stable. which significantly improves the product qualification rate and consistency.
- Full process automation: Equipped with automatic feeding, precise temperature control, efficient stirring, automatic oil draining, intelligent pan flipping and efficient oil removal system. It greatly reduces the labor intensity and human errors of workers, and improves production efficiency and product quality.
- Oil purification revolution: Food residues generated during the 100kg fully automatic chips making machines production process automatically settle and are isolated in the water layer and discharged in real time through the sewage outlet. This revolutionary design ensures that the frying oil remains fresh for a long time, prevents acidification and deterioration, greatly extends the service life of the oil, reduces oil costs, and produces healthier potato chips.
- Easy to operate, stable and reliable: The frying temperature and time can be flexibly set according to the characteristics of the product. The whole machine has a humanized design, an intuitive and easy-to-understand operation interface, stable and reliable operation, and a modern and beautiful appearance. It is an ideal upgrade choice for small and medium-sized potato chip processing companies.
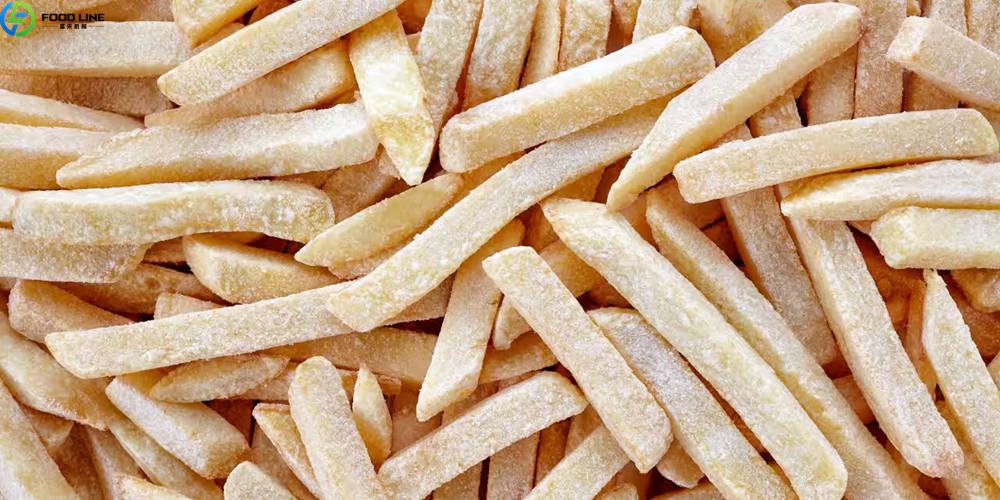
Efficient workflow
The working process of the 100kg fully automatic chips making machines as follows:
- Raw material pretreatment: The potato pieces are scrubbed, peeled, and burrs removed, and then accurately sliced using an imported slitting machine.
- Optimized shaping: After slicing, the potato chips are soaked and blanched. And then passed through an air-cooled dehydrator to remove surface moisture.
- Core frying: After dehydration, the potato chips automatically enter the fully automatic frying line. In the intelligent temperature-controlled oil pan, they are evenly heated and double-stirred to achieve perfect frying.
- Oil Draining: The fried potato chips are automatically lifted to drain the oil. And then pass through a high-efficiency vibration deoiling machine and an air-cooled deoiling line to remove excess oil to the maximum extent, achieving ideal crispness and low-oil health standards.
- Cooling and conveying: After deoiling, the potato chips are cooled down in an air cooling line to prepare for subsequent seasoning and packaging.
FAQ
No. The production line uses a humanized PLC control system, and key parameters (temperature, time) can be set on the touch screen. The automated process reduces a lot of manual intervention, is easier to operate, and shortens the employee training cycle.
Designed with ease of maintenance in mind. SUS304 material is easy to clean. Key components such as stirring paddles are removable. Smooth sewage system. Provide detailed maintenance manuals and technical support.
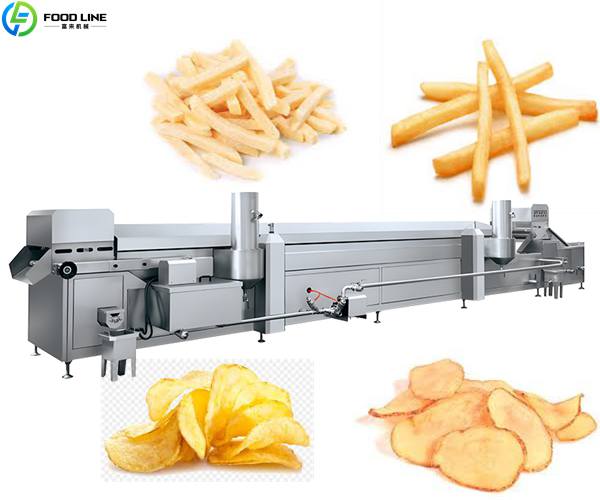
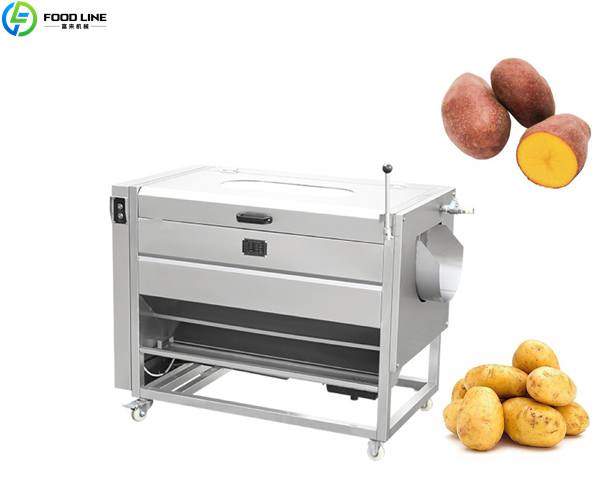
Customer Success Stories
Case 1: A small home-style processing workshop in the United States, whose products rely on traditional hand-fried, have unstable quality and high customer complaint rate. After the introduction of the 100kg fully automatic chips making machines, monthly sales and net profit margins have been greatly improved.
Case 2: After the introduction of Spanish companies, the defective rate of their potato chip products has decreased and their production efficiency has improved. The flavor improvement brought about by the improvement of oil freshness has been widely praised by consumers. And market sales have increased significantly.
Food Line Machinery
We are a large food machinery company with 20 years of experience. We choose our 100kg fully automatic chips making machines, empower traditional processes with technology, use automation to liberate manpower, and use intelligence to protect the health of oil products and product flavor. It is a production tool to improve efficiency, reduce costs and ensure quality. And it is also a unique choice for small and medium-sized food companies to seize the healthy snack market and build core competitiveness.
In addition, we are also responsible for blanching machines, frying machines, and fruit and vegetable cleaning machines.